EnLink prioritizes the health and safety of our employees, contractors, customers, and communities where we operate. Our Environmental, Health, and Safety (EHS) program focuses on mitigating risk, increasing knowledge and skills, improving processes, and measuring performance.
We invest substantial resources in our EHS efforts, and we follow industry best practices related to environmental and safety matters, in addition to applicable laws and regulations.
Employee and Leadership Responsibility
We are committed to providing safe, responsible, and ethical operations. As part of this commitment, companywide safety goals are included in our Short-Term Incentive Program, which rewards all employees for the achievement of key metrics directly tied to our strategic initiatives, via the Safety and Sustainability Scorecard (click here to learn more about our employee incentive program).
The scorecard promotes our safety-centric culture by measuring key performance indicators focused on risk management, compliance, process improvement, and employee knowledge and development, as well as contractor safety. Progress is reported to employees during monthly safety meetings, discussed quarterly in all employee calls, and available via our employee intranet.
Our EHS team hosts safety training sessions each month, with attendance required for employees based on their job position. Employees are assessed against a set of established and measurable safety goals each quarter, and company leadership reinforces the power of all employees to protect the safety of our operations, as every employee on an active job site has stop-work authority to use at their discretion.
Contractor Safety and EHS Risk Identification and Audits
We utilize process hazard analyses, pre-job tailgate meetings, inspections, and incident investigations to identify and mitigate work hazards throughout each phase of new projects and during existing operations. We conducted over 250 EHS audits and inspections in 2023. Audits are captured in our incident management system, and any concerns are addressed with our contractors and construction and engineering teams.
We also expect those we partner with, including our contractors, to focus on safety. Starting with our contractor selection process, we assess contractors’ safety programs and performance in evaluating their qualifications to do work with us. We require that our contractors receive general and site-specific safety orientations prior to working alongside our employees and in our operational facilities.
Although our contractors are responsible for their own safety and control over their work activities, we expect all our contractors to follow applicable Occupational Safety and Health Administration, Environmental Protection Agency, and Department of Transportation regulations, as well as their own established safety protocols and procedures. We encourage and expect contractors to identify and communicate risks to EnLink.
In 2023, we again held contractor safety summits in asset areas with significant contractor activity. These summits allowed us to connect with our contractors to share best practices, trends, solutions to common challenges, and safety risks facing the midstream industry.
In addition to the contractor safety summits, we have taken other steps to reinforce the importance of our GoalZERO program to our contractor companies. To begin the year, EnLink President and Chief Executive Officer Jesse Arenivas and Executive Vice President and Chief Operating Officer Walter Pinto met with the owners or executive leadership teams of our most utilized contractor companies. The purpose of these meetings was to strengthen relationships and to emphasize our commitment to worker safety.
As a result of these efforts, we achieved a contractor Total Recordable Incident Rate (TRIR)¹ of 0.58 in 2023, the lowest in EnLink history and a 40% improvement from our 2022 Contractor TRIR.
GoalZERO Program Continues to Realize Success
Our “GoalZERO” program provides tools and encouragement to help employees always strive for zero injuries, zero vehicle accidents, zero line strikes, zero fires, and zero spills. One of the most successful tools within the program is our “Take 2, Ask 3” initiative, which employees and contractors have adopted as a regular first step to getting any job done. We start every job by taking just two minutes to ask three important safety questions: “What can go wrong? What precautions should I take? Can I do this job safely?” This focuses our teams on the task at hand and helps prevent potential risks.
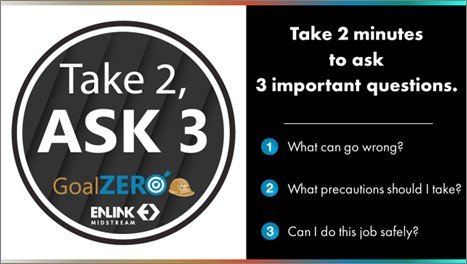
In 2023, we experienced an increase in employee injuries from 2022, which was our best safety year to date in terms of our employee injuries. Our leadership team took action to combat this trend and mitigate further injuries by hosting GoalZERO safety leadership training sessions in each asset area, encouraging employees to utilize near-miss reporting, and requiring that safety moments are shared at the start of meetings companywide. “Take 2, Ask 3” visuals were added across the company to keep this vital process top of mind. To assist in this effort, employees were given hardhat or laptop stickers, and all computer and conference room TV screensavers were updated with the three questions. At the same time, we also enhanced our root cause analysis process and shared lessons learned across the company via TV monitors to better educate employees.
This commitment to safety focus helped us to achieve a TRIR² of 0.57 by year-end 2023, which, while increased from our 2022 record-achieving performance, was 16% lower than the GPA Midstream Division 1³ average of 0.69.
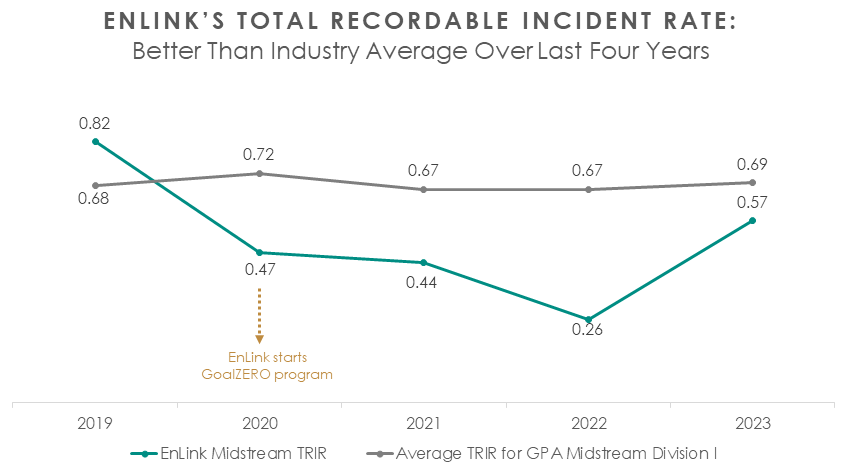
Public Safety and 811
Pipelines have a better safety record compared to other modes of transporting petroleum and natural gas products.⁴ We strive to operate our pipelines and facilities safely, reliably, and with a focus on environmental stewardship.
Through our Public Awareness Program, we provide information about our operations and safety initiatives to community members who live and work near our pipelines and facilities. We develop and distribute customized information packets each year to local communities, schools, public officials, excavation contractors, and emergency responders. To promote pipeline safety, we participated in over 80 public awareness meetings in communities across our asset base in 2023.
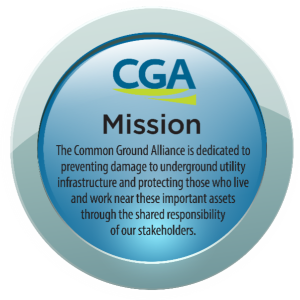
We also regularly promote digging safety through our partnership with the Common Ground Alliance, an association of underground utility companies and organizations committed to underground infrastructure safety. The Common Ground Alliance promotes the national “811” call-before-you-dig phone number, which helps professionals and homeowners safely complete digging projects by connecting them with a local “one call center” that can identify and mark approximate locations of underground utility lines. Once lines are flagged, the project can begin, and underground lines can be safely avoided. In 2023, EnLink cleared or located lines for over 134,000 tickets assigned to the company via the 811 system, with 100% of these tickets cleared on time.
Driving Safety
Driving safety is always a focus area for us. We believe that driving is one of the most hazardous parts of our jobs and our commitment to safe driving is one way that we can keep our employees and communities safe. This focus begins as employees join our team and take an initial driver safety training through the National Safety Council. After the initial training, safe driving habits are reinforced through periodic hands-on training and more frequently through safety meeting topics. In 2023, we achieved a preventable vehicle accident rate⁵ of 1.08, the lowest in our history and 32% lower than our 2022 performance. We achieved this record while driving 12.9 million miles.
- Calculated by multiplying the number of contractor recordable incidents by 200,000 work hours and dividing by the total actual work hours of contractors while working for EnLink.
- EnLink calculates TRIR by multiplying the number of recordable injuries by 200,000 work hours and dividing by EnLink's total actual work hours.
- The GPA Midstream Association classifies companies that complete 1 million or more midstream operational workhours in one year as Division I.
- “Transportation Accidents by Mode,” U.S. Department of Transportation: https://www.bts.dot.gov/content/transportation-accidents-mode.
- Calculated by multiplying the number of preventable vehicle accidents by 1,000,000 miles and dividing by the total actual miles driven by EnLink employees. A preventable vehicle accident is an automobile accident (whether or not involving a third party) in which the driver of a company vehicle is at-fault or did not operate the vehicle in a safe manner which led to the accident.
More in the "Responsible Operations" section:
- Responsible Operations Overview
- Energy Use and Emissions
- Carbon Solutions
- Environmental Performance and Stewardship
- Emergency Preparedness
- Asset Integrity Management
- Operational Excellence
Other sections:
The information and data (collectively, “Information”) provided in EnLink’s 2023 Sustainability Report (“Report”) reflects content as of and for the period ending December 31, 2023, unless otherwise indicated. Such Information in this Report is for informational purposes only. EnLink does not make, and hereby expressly disclaims, any representation or warranty as to the accuracy or completeness of the Information contained herein. This Report is being published on August 6, 2024, and EnLink undertakes no obligation or duty to (1) update or correct the Information, (2) provide additional details regarding the Information, or (3) continue to provide the Information, in any form, in the future. EnLink reserves the right, in its sole discretion, to modify, update, change, delete, or supplement the Information from time to time without notice. The Information should not be interpreted as any form of guaranty or assurance of future results or trends. EnLink is expressly not incorporating by reference any of the Information into any filing of EnLink made with the United States Securities and Exchange Commission or in any other filing, report, application, or statement made by EnLink to any federal, state, or local governmental authority. This Report contains information based upon EnLink’s role in the broader economy, environment, and society and is presented for the purpose of responding to issues that are important to a wide range of interested parties. While events, scenarios, and efforts discussed in this report may be significant, any significance should not be read as necessarily rising to the level of materiality pertaining to disclosures required under U.S. federal securities laws, which have distinct and specific concepts of materiality.